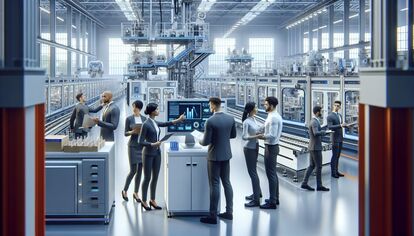
Manufacturing companies in the pharmaceutical, cosmetic, and food & beverage industries often struggle with maintaining consistent quality and minimizing defects, leading to costly recalls and damage to their reputations.
Follow these tips to enhance your processes through automation and ensure high-quality production:
1. Quality Control
Manufacturers that neglect stringent quality control measures face increased defect rates and customer dissatisfaction. Implementing automated quality inspections can significantly alleviate these issues.
- Implement a Vision System: Integrate a Cognex vision system to consistently detect defects in real-time, ensuring that only high-quality products reach your customers.
- Utilize Machine Learning: Leverage advanced algorithms to analyze inspection data and refine quality control processes continually, resulting in fewer errors over time.
- Establish Standard Operating Procedures: Create robust SOPs that incorporate automated quality checks, fostering a culture of accountability and precision in production lines.
2. Production Efficiency
Manufacturers frequently encounter bottlenecks in production due to manual processes, leading to delays and increased labor costs. Automation can streamline workflows and boost overall efficiency.
- Optimize Workflow Layout: Reconfigure your production line with automated systems for better flow, reducing handling times and minimizing downtime.
- Integrate Robotics: Deploy robots for repetitive tasks, which allows human workers to focus on more complex responsibilities, enhancing productivity levels.
- Monitor Production Metrics: Utilize real-time data analytics to identify inefficiencies and adjust processes quickly, ensuring optimal output.
3. Waste Reduction
Excess waste in manufacturing not only increases costs but also negatively impacts environmental sustainability efforts. Automation technologies can help minimize material waste effectively.
- Implement Precise Material Handling: Use automated guided vehicles (AGVs) for accurate transfer of materials, reducing the likelihood of damage and waste.
- Adopt Predictive Maintenance: Predictive analytics can reduce equipment failures and minimize waste due to unplanned downtime, maximizing resource utilization.
- Recycle and Repurpose Materials: Establish automated systems for sorting waste, allowing for efficient recycling and repurposing of materials within your operations.
4. Data-Driven Decisions
Relying on intuition rather than data can lead manufacturing companies to make costly mistakes in operations. Automation can empower organizations with actionable insights through data analytics.
- Utilize Real-Time Analytics: Implement systems that provide real-time data on production metrics, helping teams make informed decisions quickly and efficiently.
- Establish Key Performance Indicators (KPIs): Define KPIs relevant to your production processes, and use automation to track these metrics, fostering continuous improvement.
- Leverage Reporting Tools: Use automated reporting tools for a comprehensive view of operations, allowing for better strategic planning and resource allocation.
5. Scalability
Growing manufacturing businesses often face challenges in scaling their operations without compromising quality or efficiency. Automation provides the ability to scale effectively and sustainably.
- Design Flexible Manufacturing Systems: Create systems that can easily adapt to increased production demands without the need for major overhauls.
- Invest in Modular Automation Solutions: Utilize modular systems that allow for easy integration of additional capabilities as your business grows, ensuring a smooth scaling process.
- Continuous Training and Development: Provide ongoing training for employees on new automated technologies to ensure that your workforce is prepared for expansion.