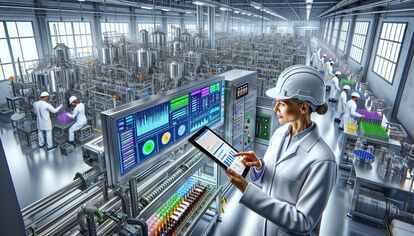
Manufacturing companies in the pharmaceutical, cosmetic, and food & beverage sectors often struggle with low yield due to inefficiencies in their processes, resulting in significant losses. With rising competition and increasing consumer demand, addressing these low-yield issues is imperative to drive profitability and growth.
Follow these tips to identify and resolve the underlying causes that may be affecting your yield:
1. Inefficient Quality Control
Inefficient quality control processes can lead to increased defects and waste, resulting in a lower overall yield. To combat this challenge, consider implementing more effective inspection solutions.
- Optimize Inspection Processes: Streamlining your quality control protocols with automation can significantly reduce error rates and improve product quality.
- Utilize Cognex Vision Systems: Implementing advanced vision systems can enhance defect detection, ensuring that only the highest quality products make it to consumers.
- Integrate Automated Reporting: Automated reporting tools can provide insights into the quality control process, helping teams identify areas for improvement quickly.
2. Lack of Real-time Data
Without real-time data, production teams may miss early warning signs of inefficiencies that can lead to decreased yield. Access to immediate insights can transform decision-making processes.
- Implement Data Analytics Tools: Utilize analytics to gain insights from your production data in real-time, allowing you to react swiftly to any issues.
- Leverage IoT Integration: Connect your equipment and systems to gather valuable data that can improve real-time visibility across the manufacturing process.
- Employ Predictive Maintenance Techniques: Use data-driven maintenance strategies to prevent equipment failures before they impact production yield.
3. Inadequate Maintenance
Neglecting regular maintenance can result in unplanned downtimes, significantly impacting overall production yield. An effective maintenance strategy can mitigate these risks.
- Establish a Maintenance Schedule: Regularly scheduled maintenance prevents equipment malfunctions and improves the longevity of your production machinery.
- Invest in Predictive Maintenance Tools: Employ technologies that monitor equipment health in real-time to forecast potential failures and schedule repairs proactively.
- Train Staff on Maintenance Practices: Educate your team on essential maintenance practices to ensure they can identify issues before they affect production yield.
4. Insufficient Training
Staff members lacking adequate training can contribute to operational inefficiencies and non-compliance with production standards, leading to lower yield. Investing in robust training programs is vital.
- Develop Comprehensive Training Programs: Create structured training that covers both equipment usage and best practices for production processes.
- Utilize Hands-on Experience: Provide opportunities for employees to engage in hands-on training to solidify their understanding and skills.
- Offer Continuous Learning Opportunities: Encourage ongoing education to keep staff updated on the latest technologies and methodologies in manufacturing.
5. Misconfigured Automation
Automation misconfigurations can lead to inconsistencies in production, causing reduced efficiency and lower overall yield. Properly programmed and configured automation is vital for success.
- Regularly Audit Automation Settings: Conduct periodic audits of your automated systems to ensure configurations align with your production goals.
- Seek Expertise for Configurations: Collaborate with specialists to ensure your automation solutions are tailored to meet specific production requirements.
- Utilize Simulation Tools: Before implementing changes, use simulation tools to visualize the impacts of updated automation configurations on production yield.
6. Production Misalignment
When production processes are misaligned, it can create bottlenecks that lead to inefficiencies and lost yield. Ensuring alignment across all stages of production is key to maximizing output.
- Conduct Workflow Assessments: Regular assessments help identify misalignments in the production line that could be hindering yield.
- Integrate Cross-Department Collaboration: Foster communication among teams to enhance synchronization and streamline production efforts.
- Adjust Production Schedules Based on Data: Use real-time data to make informed adjustments to production schedules, ensuring optimal alignment and efficiency.