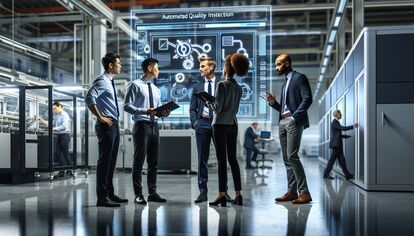
Manufacturers in the pharmaceutical, cosmetic, and food & beverage industries that fail to evaluate their existing processes often face increased defects, waste, and downtime, jeopardizing their yield and quality. These issues can lead to significant economic losses and harm your reputation in a competitive market.
Follow these steps to refine your operations and enhance productivity:
1. Evaluate Processes
Many manufacturing processes are outdated or inefficient, leading to unnecessary waste and defects. To remedy this, it's essential to conduct a thorough evaluation of your current workflows.
- Conduct Process Mapping: Visualizing your processes can help identify bottlenecks and redundancies. This clarity enables you to focus on specific areas for improvement.
- Implement Lean Principles: Adopting Lean methodologies can streamline your operations and eliminate waste. This approach encourages a culture of continuous improvement within your team.
- Engage Stakeholders: Collaborating with team members who are hands-on in the processes can yield valuable insights. Their input is vital in designing more efficient workflows.
2. Implement Quality Inspection
Without automated quality inspection, defects can slip through, leading to costly recalls and customer dissatisfaction. Introducing effective inspection solutions is crucial for maintaining high standards.
- Integrate Vision Systems: Utilizing Cognex vision systems can enhance your inspection capabilities, ensuring that every product meets quality benchmarks. This automation reduces human error and boosts efficiency.
- Standardize Inspection Protocols: Establishing consistent quality inspection protocols helps in minimizing disputes and errors. It instills confidence in your output quality among clients and stakeholders.
- Leverage Real-time Feedback: Implementing real-time data from inspections facilitates immediate corrective actions. This swift response enhances overall product quality and operational efficiency.
3. Use Data Analytics
Many manufacturers overlook the potential of data analytics, which can reveal hidden inefficiencies and trends. Adopting a data-driven approach enables informed decision-making.
- Collect Process Data: Gathering data from various points in your production line can provide insights into performance trends. Analyzing this data can inform necessary adjustments to optimize your operations.
- Utilize Predictive Analytics: Employing predictive models can help anticipate potential failures or defects before they occur. This proactive approach minimizes downtime and improves product reliability.
- Benchmark Performance Metrics: Comparing your data against industry standards can highlight areas needing improvement. This benchmarking allows you to strive for best practices within your sector.
4. Train Your Team
Even the best systems and processes can underperform without a knowledgeable team. Investing in training ensures that your workforce is equipped to leverage new technologies and methodologies effectively.
- Conduct Regular Workshops: Hosting training sessions can keep your team updated on the latest industry practices. This commitment to education fosters a culture of continuous improvement.
- Encourage Certification Programs: Promoting certifications related to quality control or manufacturing technologies can empower your workforce. Skilled employees significantly enhance operational output and quality.
- Implement Cross-Training: Ensuring your team is skilled in multiple areas increases flexibility and resilience. This adaptability can dramatically boost productivity during peak production times.
5. Monitor Performance
Failing to track key performance indicators can lead to undetected issues that affect productivity and quality. Consistent monitoring is vital for sustained improvement in manufacturing processes.
- Establish KPIs: Defining clear key performance indicators allows for focused monitoring of your processes. Regularly reviewing these metrics highlights trends and areas needing attention.
- Utilize Dashboards: Implementing visualization tools such as dashboards can simplify data interpretation. This technology makes it easier for decision-makers to grasp performance at a glance.
- Conduct Regular Reviews: Scheduling periodic reviews of your performance data ensures ongoing assessment and optimization. This iterative process fosters a commitment to excellence.