Vision Inspection Systems Using Machine Vision
An automatic inspection system using machine vision technology revolutionizes the quality control processes in various manufacturing industries everywhere. By combining advanced hardware and sophisticated software algorithms, these systems enable precise and reliable inspection of products, components, or materials, ensuring adherence to predefined quality standards.
In manufacturing environments, an automatic vision inspection system plays a crucial role by automating the inspection process and reducing dependency on manual labor. It employs high-resolution cameras, high-speed cameras, lighting techniques, smart cameras, and image processing algorithms to capture and analyze images of the items under the vision inspection systems. The vision inspection system then evaluates key attributes such as dimensions, color, shape, texture, and surface scratches, detecting any anomalies or variations from the expected specifications.
Understanding Machine Vision Systems Technology
Vision inspection systems technology is the core technology behind automatic inspection and measurement systems. It enables machines to emulate human vision, interpreting and understanding visual information for a wide range of applications. Using digital imaging and specialized imaging techniques, vision inspection systems capture images or video frames, which are then processed and analyzed by powerful algorithms.
Overall, understanding machine vision technology development is essential to grasp the development, underlying principles, development and capabilities of an automatic inspection system, highlighting its potential for enhancing quality control processes and streamlining manufacturing line operations.
Benefits of Implementing in Inspection Processes
Heightened precisionand quality control
The implementation of machine vision technology in inspection processes brings forth a myriad of benefits for industries across the board. One of the primary advantages is the heightened precisionand quality control it offers.
Machine vision inspection systems can detect even the minutest defects or variations, ensuring that every product meets the required specifications.
Increased efficiency and cost savings
Another significant benefit is the increased efficiency and cost savings that come with the automation of inspection processes on production lines. By automating the inspection tasks that were traditionally done manually, machine vision systems eliminate the need for human operators to perform repetitive and time-consuming inspections of production lines.
Reduction of manual labor and human error
Furthermore, machine vision inspection systems contribute to the reduction of manual labor and human error. Human inspection is prone to inconsistencies and errors due to factors such as fatigue, distraction, or subjectivity.
Vision inspection system the Key Components
An automatic inspection vision system often comprises several key components that work in harmony to deliver accurate and reliable inspection results consistently. These components form the foundation of the vision inspection system, and include cameras, lighting equipment, and image processing capabilities.
Cameras
Cameras are a fundamental imaging component of an automatic inspection system as they capture images or video frames of the objects under inspection. These cameras can vary in type, such as area scan cameras or line scan cameras, depending on the application requirements. Advanced cameras, including high-speed cameras, have high-resolution imaging capabilities at rapid speeds, allowing for the capture of detailed images for precise object analysis.
Lighting
Lighting is another essential component that ensures optimal illumination of the objects being inspected. Proper lighting plays a crucial role in enhancing image quality, reducing shadows, and improving contrast, enabling the camera to capture clear and accurate images. Different types of lighting and ambient light sources, such as LED lights or fiber optic illuminators, may be utilized to cater to the specific requirements of the task.

Image processing
Image processing capabilities are at the heart of an automatic inspection system. After the images are captured, sophisticated image processing algorithms are employed to analyze and interpret the visual data. These algorithms apply various techniques, such as edge detection, pattern recognition, or machine learning, to extract meaningful information from the images. The processing unit executes these algorithms to identify surface defects within, measure dimensions, classify objects, or perform any other required inspection tasks.
Applications of Machine Vision in Quality Control
These are just a few examples of how machine vision technology revolutionizes across industries. By implementing machine vision systems, businesses in the food and pharmaceutical industries can enhance their manufacturing operations, reduce defects, and improve product quality, ultimately strengthening their industry and competitive edge.
Automotive
The automotive industry utilizes machine vision systems for inspections throughout the manufacturing process. Machine vision systems can examine components for defects, ensure proper assembly, and verify critical measurements. This ensures that only high-quality automotive parts make it into the final products, improving safety, reliability, and customer satisfaction.
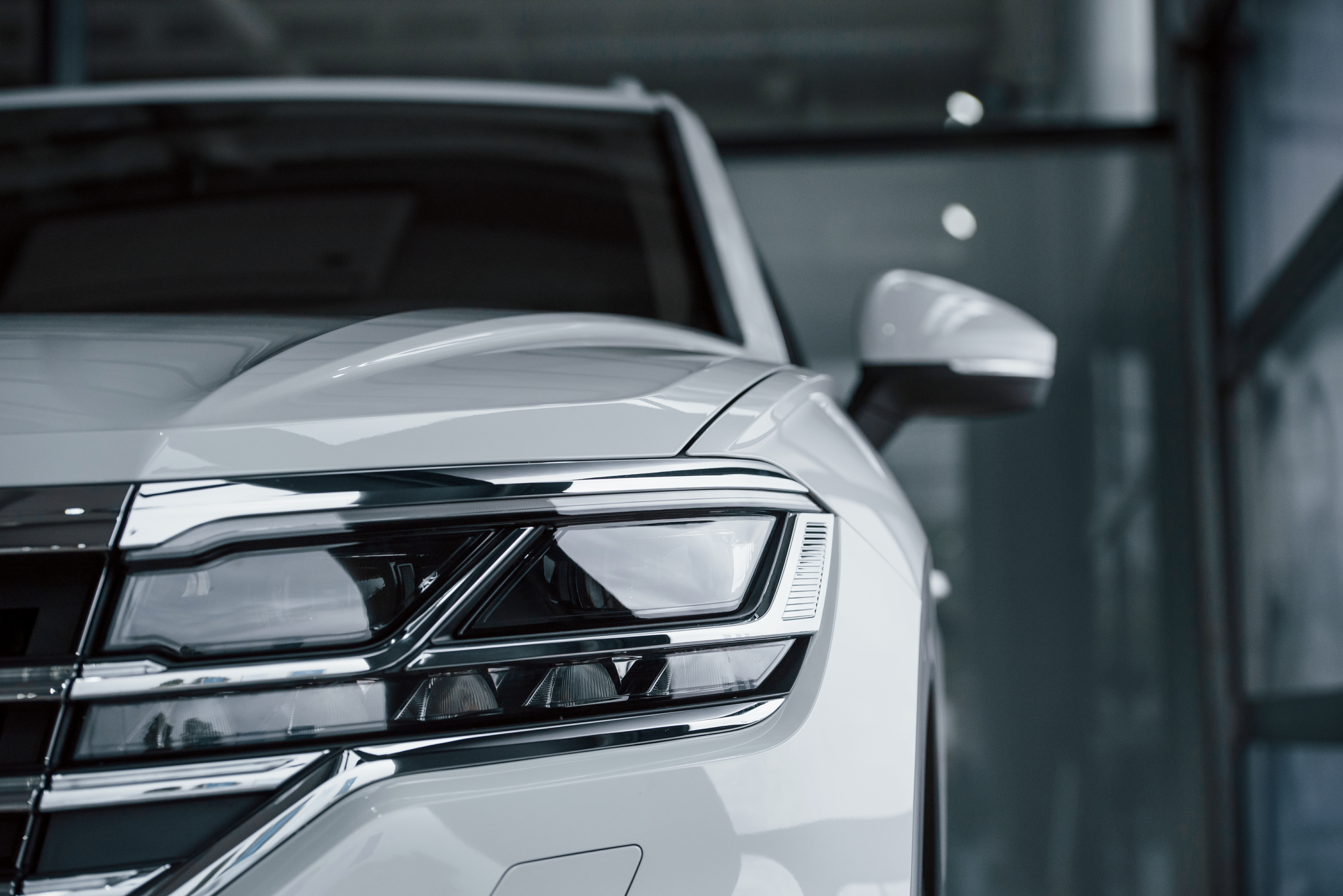
Food and pharmaceutical
In the food and pharmaceutical industry for example, machine vision plays a crucial role in solutions by inspecting tablets, capsules, or medical devices for imperfections or errors in packaging. These systems can detect inconsistencies functional flaws in color, shape, size measurement, or contamination, ensuring that only compliant and safe products reach the market.
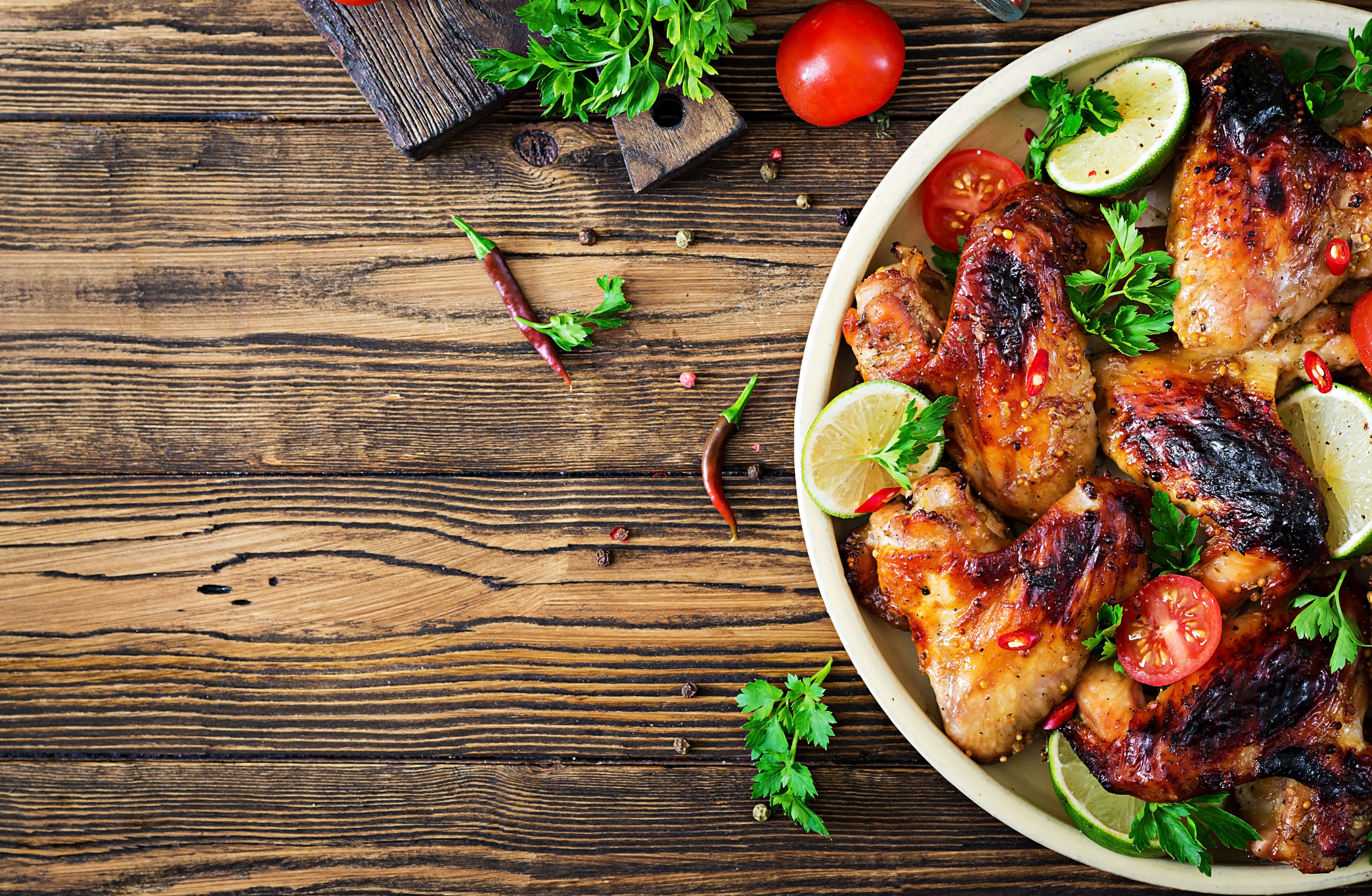
Electronics and manufacturing
Furthermore, machine vision is extensively used in electronics and manufacturing industries. It is employed in the inspection of printed circuit boards (PCBs), ensuring the correct placement and soldering of components. Machine vision systems can identify missing or misaligned components, soldering defects, or PCB defects, allowing for timely solutions and minimizing the risk of faulty electronics entering the market.
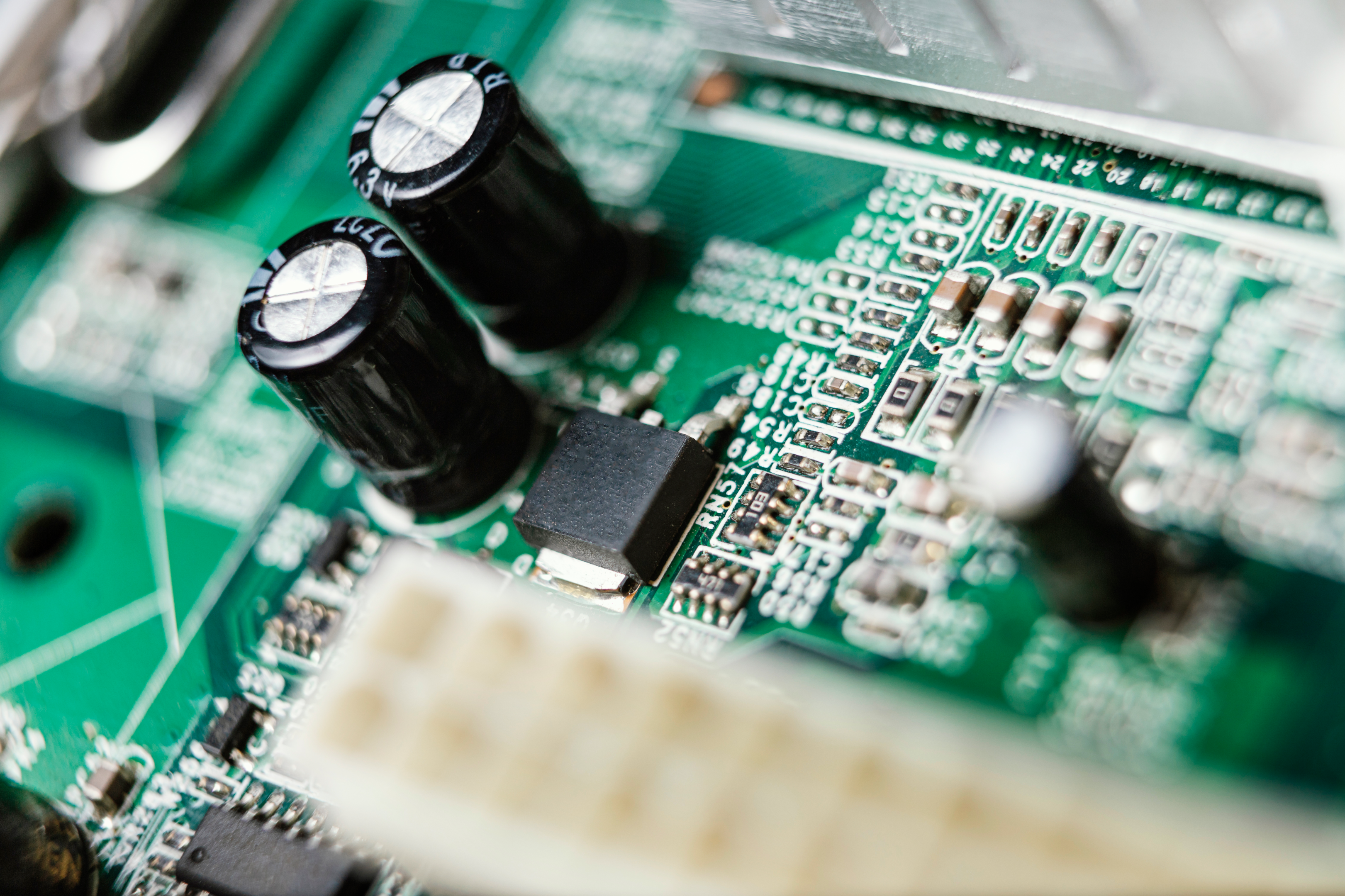
Factors to Consider When Choosing a Vision System
When it comes to selecting a vision system for your specific application, several factors should be carefully considered. One of the primary factors is the performance requirements and specifications. Different applications may require varying levels of accuracy, speed, or resolution. It is crucial to assess your specific needs and choose a whole vision system that aligns with those requirements to ensure optimal performance and reliable inspection results.
Scalability and flexibility are also essential considerations. As your food and business grows or your inspection needs evolve, it is important to choose a machine vision system that can scale accordingly. The same vision system used should be able to handle increasing volumes, accommodate different product sizes or packaging types, and adapt to changing inspection criteria or standards.
Cost-effectiveness and return on investment (ROI) play a significant role in decision-making. While investing in a high-quality machine vision system might incur upfront costs, it is important to evaluate the potential long-term savings it can bring. Consider factors such as labor cost reductions, decreased rework or waste, and improved product quality. A thorough cost-benefit analysis should be performed to determine the whole vision system's ROI over its lifespan.
Another factor to consider is the ease of integration and compatibility with existing equipment, software or systems. Seamless integration with your production line is crucial to ensure efficient operation and minimal disruption. The machine vision system installed should be compatible with your automation setup and have the necessary interfaces or protocols to communicate with other front line components or software tools.
Troubleshooting Common Challenges in Automatic Inspection Systems
While automatic inspection systems offer remarkable advantages, they can sometimes encounter common challenges that need to be addressed.
One of the common issues is lighting and image contrast. Poor lighting conditions, incorrect placement of lighting sources, or inadequate contrast can affect the quality of captured images, making it difficult for the system to detect defects accurately. Optimizing lighting techniques, adjusting angles, or using different types of lighting sources can help overcome these challenges.
False positives and false negatives are another challenge commonly faced in automatic inspection systems. False positives occur when the system wrongly identifies non-defective products as defective, leading to unnecessary rejections and increased cost.
False negatives, on the other hand, occur when the system fails to detect actual defects, allowing defective items to pass through the inspection. Fine-tuning the system's detection algorithms, adjusting threshold values, or ensuring proper calibration can help minimize these errors and thus improve efficiency and overall precision across multiple inspections.
Calibration and setup problems can also hinder the performance of automatic inspection systems. Proper calibration of photographic device, lenses, and other components is essential to achieve accurate and consistent results. Any misalignment or incorrect settings can introduce errors in the inspection process. Regular maintenance, calibration checks, and accurate setup can overcome these challenges and ensure reliable performance.
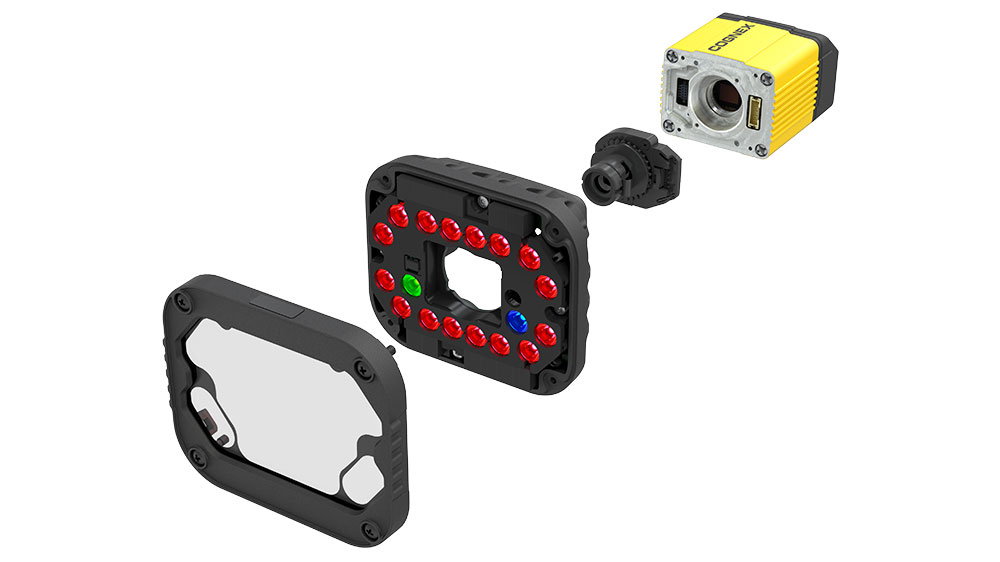
Successful Implementation
Several real-world case studies demonstrate the successful implementation of machine vision in inspection processes, showcasing the tangible benefits it brings to various industries. One such case study involves a manufacturing company that integrated machine vision systems to inspect their products for quality control purposes.
By automating the inspection and manufacturing process together, they significantly reduced the time required for inspections and achieved a remarkable increase in precision, resulting in a drastic reduction in defective products reaching the market. This implementation not only enhanced their brand reputation but also led to substantial cost savings by avoiding recalls and rework.
In another case study, a pharmaceutical company adopted machine and vision inspection systems technology to inspect blister packs for medication. The machine vision inspection system efficiently detected any packaging defects, such as improper sealing, missing tablets, or incorrect product labeling throughout.
By implementing this automated inspection process, they ensured compliance with regulatory standards, mitigated potential safety risks, and improved overall product quality. This successful integration of machine and vision inspection systems not only minimized the possibility of non-compliant products but also streamlined the production line, resulting in increased throughput.
A third case study focuses on a electronics manufacturing company that utilized vision systems to inspect printed circuit boards (PCBs). By automating the inspection process, they reduced the time required for manual inspections and enhanced their quality control efforts.
The machine vision system accurately identified defects such as short circuits, missing components, or soldering issues, enabling timely corrections and improving overall product reliability. This implementation led to remarkable improvements in production efficiency, reduced scrap rates, and ultimately enhanced customer satisfaction.
Comparison of Automated Inspection Systems and Traditional Methods
When considering inspection methods, including the vision inspection solutions and systems and solutions like Keyence vision systems, it is crucial to compare and evaluate the advantages and limitations of automated vision inspection solutions and keyence vision systems, versus traditional methods.
Automated Inspection Systems
With advanced algorithms, software tools and high-speed photographic device, automated inspection systems enhance productivity, reduce production cycle times, and ensure the high accuracy of assessments. Moreover, these systems offer the ability to capture and analyze extensive data, facilitating detailed insights and process optimization for
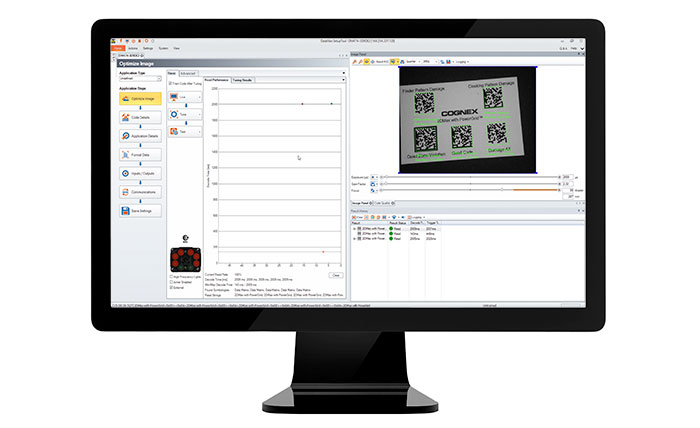
manufactured products.
Traditional Methods
While manual inspections may have their place in certain tasks or smaller-scale operations, they often prove to be labor-intensive, time-consuming, and prone to errors. The limitations of traditional methods become evident when compared to the speed, precision, and consistency offered by automated inspection systems, particularly in the context of determining the orientation position and positioning position of products.