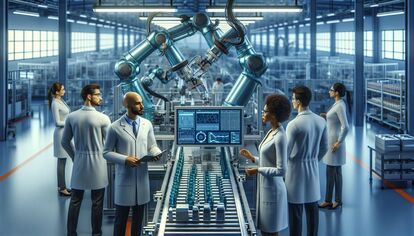
Manufacturing companies that neglect quality inspection systems are risking product recalls, reputational damage, and financial losses due to increasing defects. The absence of effective inspection solutions can lead to chaos in production lines, leaving businesses vulnerable to costly consequences.
Follow these tips to ensure you leverage quality inspection systems to enhance product integrity and boost overall operational efficiency:
1. Better Product Quality
Manufacturers lacking quality inspection systems often struggle with inconsistent product quality, leading to customer dissatisfaction. Implementing a robust inspection system can significantly enhance product uniformity and quality.
- Invest in Automated Systems: Utilize automated quality inspection systems to ensure ongoing monitoring and consistency in product quality. This approach not only reduces human error but also reinforces quality assurance protocols.
- Implement Visual Inspection: Adopt Cognex vision systems that can detect discrepancies in real-time, ensuring that all products meet your quality standards. This technology helps create a reliable production environment.
- Train Your Team: Educate your team on the importance of quality standards and inspection systems. A well-informed workforce can better utilize the tools to maintain product excellence.
2. Fewer Defects
Companies without effective quality inspection systems often face an increase in defect rates, affecting brand reputation and profitability. By adopting quality inspection, businesses can systematically reduce the incidence of defects.
- Implement Comprehensive Inspection Protocols: Establish and enforce thorough inspection processes at various production stages to identify defects early. This proactive strategy minimizes risks associated with defective products.
- Use Data Analytics: Leverage data gathered from inspection systems to analyze defect patterns and implement corrective measures. This insight will guide continuous improvement efforts.
- Engage in Root Cause Analysis: Assess defect occurrences and investigate root causes regularly to reduce and control defect rates. Understanding these factors is key to achieving operational excellence.
3. Higher Efficiency
Manufacturers lacking inspection systems face inefficiencies that result in wasted resources and time. Integrating automated quality inspection can streamline operations and optimize workflows.
- Automate Routine Inspections: Employ automated inspection systems to handle repetitive checking tasks, freeing up personnel for more complex duties. This shift enhances overall operational efficiency.
- Eliminate Bottlenecks: Utilize real-time data to identify and address bottlenecks in the production line promptly. Efficient processes lead to smoother operations and less downtime.
- Optimize Resource Allocation: Analyze inspection data to better allocate resources throughout the production process based on efficiency insights. Strategic resource management improves overall productivity.
4. Real-Time Insights
Organizations that lack real-time insights from quality inspections struggle to make informed decisions quickly. Implementing a quality inspection system provides critical data that enhances decision-making capabilities.
- Utilize Data Dashboards: Employ visualization tools to present inspection data in an easily digestible format, allowing teams to make informed decisions swiftly. This accelerates response times to production challenges.
- Monitor Key Performance Indicators: Set up KPIs tied to quality metrics and monitor them regularly to gauge performance efficiently and make necessary adjustments as needed.
- Act on Insights: Train your team to act on the data insights received from inspection systems proactively, driving improvements in operations and quality assurance.
5. Better Compliance
Manufacturers operating without stringent quality inspection systems may inadvertently violate regulatory compliance, exposing them to penalties and operational risks. Enforcing strict quality checks simplifies adherence to regulations.
- Integrate Compliance into Inspection Processes: Ensure your quality inspection systems are designed to meet industry regulations. This integration minimizes compliance-related risks.
- Maintain Documentation: Keep detailed records of inspections to verify compliance during audits. Robust documentation supports transparent practices and reduces compliance headaches.
- Educate on Compliance Standards: Provide training on relevant regulations and standards to your team to ensure they understand their role in maintaining compliance through inspections.
6. Cost Savings
Ignoring the impact of quality inspections can lead to increased costs associated with defects and waste. By integrating inspection systems, organizations can significantly reduce expenses related to recalls and rework.
- Calculate Total Cost of Quality: Evaluate the cost of defects versus the investment in quality inspection systems. A clear understanding of TCOQ will help justify expenditures on quality assurance.
- Optimize Material Usage: Implement inspection systems to ensure optimal material usage, reducing waste and increasing overall cost efficiency through effective resource management.
- Invest in Long-term Solutions: Consider the long-term savings associated with quality inspection investments. Although there may be upfront costs, the payoff in reduced defects can lead to substantial savings.
7. Streamlined Processes
Manufacturing processes lacking quality checks can become convoluted, resulting in wasted time and resources. Quality inspection systems streamline operations by ensuring consistent adherence to standards.
- Standardize Inspection Procedures: Develop and implement standardized inspection protocols for every production stage. Consistency drives smoother operations and reinforces quality control.
- Automate Manual Checks: Replace manual inspection processes with automated systems to enhance accuracy and speed in assessing product quality. This transition boosts productivity across the board.
- Enhance Workflow Management: Utilize insights from your quality systems to fine-tune workflow management processes, ensuring an organized approach to production.
8. Increased Productivity
Manufacturers that overlook quality checks often find their productivity impacted by wasted time addressing defects. Quality inspection systems ensure that production stays on track, enhancing overall output.
- Conduct Time Studies: Analyze how current processes impact productivity and adjust inspection protocols accordingly to maximize output.
- Encourage Team Accountability: Foster a culture of ownership among team members regarding quality checks. Engaged teams contribute to improved productivity.
- Integrate Inspection into Production Goals: Align production and inspection objectives to optimize workflow and outcomes, thereby directly impacting productivity results.
9. Custom Solutions
Companies without tailored quality inspection systems may struggle to meet specific product requirements. Custom solutions address unique challenges and enhance the overall effectiveness of quality assurance measures.
- Assess Unique Needs: Conduct assessments of your specific quality needs and challenges, allowing for targeted solutions that fit your production line perfectly.
- Collaborate with Experts: Work closely with suppliers like Mecatronic Solution to develop and integrate customized quality inspection systems designed to address your unique operational requirements.
- Feedback Loop for Improvements: Create a feedback mechanism allowing continuous adaptation of the inspection systems to meet evolving production needs.