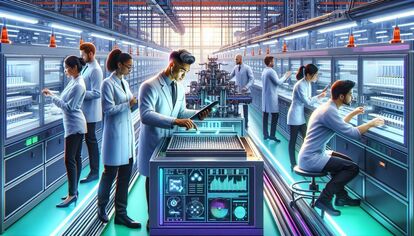
Manufacturers in the pharmaceutical, cosmetic, and food & beverage industries often grapple with inconsistent raw materials that lead to product failures, jeopardizing reputation and profitability. By addressing these challenges head-on, you can ensure higher product quality and customer satisfaction.
Follow these tips to ensure you tackle the challenges effectively:
1. Inconsistent Raw Materials
Inconsistent raw materials can result in defects that compromise product quality. To combat this issue, follow the recommendations below.
- Standardize Supplier Selection: Choose suppliers that adhere to strict quality standards and regularly assess their materials to eliminate variability.
- Implement Incoming Quality Control: Establish inspection protocols for incoming materials to identify defects before production begins.
- Communicate with Suppliers: Foster open communication with your suppliers about quality expectations and collaborate on improvement initiatives.
2. Lack of Real-Time Monitoring
A lack of real-time monitoring can lead to undetected quality issues during production, resulting in significant waste. Utilize the following recommendations to improve monitoring.
- Invest in Automation Technology: Use automated quality inspection systems to monitor processes continuously and identify defects in real-time.
- Implement Data Analytics: Analyze production data to spot trends and anomalies that might indicate quality issues.
- Set Up Alerts for Deviations: Create alert systems that notify your team immediately when quality parameters are breached.
3. Complex Production Processes
Complex production processes can introduce variability that negatively impacts quality control. Leverage these tips to streamline operations.
- Simplify Workflows: Assess production workflows and eliminate unnecessary steps to enhance efficiency and minimize errors.
- Use Visual Work Instructions: Implement visual guides to assist operators in maintaining consistency throughout the production process.
- Conduct Process Mapping: Map out each stage of production to identify complexities and develop solutions to reduce them.
4. Insufficient Team Training
Insufficient team training can lead to inconsistent quality and operational errors. Address this issue with the suggestions outlined below.
- Develop Comprehensive Training Programs: Create training programs that cover quality control best practices and the use of inspection technologies.
- Implement On-the-Job Training: Pair new employees with experienced team members for hands-on learning that reinforces quality standards.
- Continuously Evaluate Training Needs: Regularly assess your team's knowledge to identify gaps and update training accordingly.
5. Implementing Quality Inspections
Implementing quality inspections can be challenging, leading to overlooked defects. Utilize the following recommendations to enhance your inspection process.
- Integrate Automated Inspection Systems: Use automated vision systems that provide consistent and accurate quality assessments.
- Establish Inspection Checkpoints: Set key inspection points throughout the production process to catch defects early.
- Train Staff on Best Practices: Ensure staff are trained on proper inspection methods to standardize quality checks.
6. Regulatory Compliance Issues
Failure to comply with regulations can result in costly penalties and product recalls. Address compliance challenges with these strategies.
- Stay Updated on Regulations: Regularly review industry standards and regulations to ensure compliance in all manufacturing practices.
- Conduct Internal Audits: Perform routine audits to identify compliance gaps and address them proactively.
- Use Quality Management Systems: Implement software solutions to help track compliance and produce necessary documentation easily.
7. System Integration Challenges
System integration challenges can hinder the efficiency of quality management systems. Follow these recommendations to streamline integration.
- Choose Compatible Technologies: Prioritize systems that seamlessly integrate with existing technologies in your manufacturing line.
- Engage in Cross-Department Collaboration: Foster communication between departments to ensure smooth integration of quality systems.
- Consult with Integration Experts: Work with system integrators to address potential integration issues and achieve optimal results.
8. Resistance to Technology Adoption
Resistance to adopting new technology can stall quality improvement efforts. Combat this challenge with effective strategies.
- Communicate Benefits Clearly: Clearly outline how new technologies enhance quality and efficiency to gain buy-in from your team.
- Provide Hands-On Demonstrations: Offer demonstrations that allow team members to experience the benefits of new technologies firsthand.
- Encourage Feedback: Create an open forum for team members to discuss their concerns about new technology to facilitate a smoother transition.