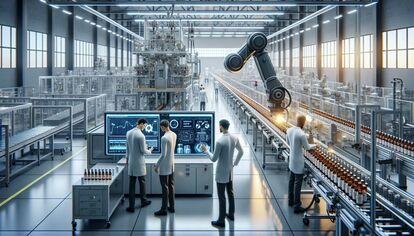
Northern American manufacturing companies in the pharmaceutical, cosmetic, and food & beverage industries that struggle with fluctuating quality inspection results often face increased defects, waste, and production delays. The consequences of inadequate inspection processes can severely impact overall product quality and profitability.
Follow these tips to establish key indicators for quality inspection success and enhance your manufacturing outcomes:
1. Inspection Consistency
Manufacturers often encounter variability in inspection results, leading to inconsistent product quality and potential regulatory issues. To address this, consider implementing robust quality control measures.
- Standardize Operating Procedures: Document and enforce standardized operating procedures to ensure uniformity in inspection processes across all shifts and operators.
- Utilize Automated Solutions: Deploy automated vision systems to minimize human error and maintain consistent inspection standards throughout the production process.
- Conduct Regular Audits: Regularly review inspection processes and outcomes to ensure adherence to established standards and identify opportunities for improvement.
2. Defect Rate Reduction
High defect rates can lead to increased rework, wasted materials, and unsatisfied customers, ultimately hurting profitability. Implementing effective defect detection methods is essential to minimize these challenges.
- Employ Advanced Vision Technology: Leverage cutting-edge vision systems that offer high accuracy and reliability in detecting defects early in the production line.
- Analyze Defect Patterns: Implement data analysis solutions to monitor defect trends over time, allowing for proactive measures to be taken.
- Implement Root Cause Analysis: Conduct thorough investigations to determine the root causes of defects, allowing for targeted improvements to be made.
3. Manufacturing Yield
Manufacturing yield reflects the ratio of good products to total products produced, and low yield rates can indicate underlying quality issues. Improving yield is crucial for maximizing profitability.
- Monitor Yield Metrics: Regularly track manufacturing yield metrics to identify fluctuations and address potential disruptions.
- Optimize Production Processes: Continuously refine manufacturing processes to minimize waste and improve overall yield.
- Implement Predictive Maintenance: Use predictive maintenance strategies to ensure equipment is functioning optimally, thereby supporting consistent yield rates.
4. Overall Equipment Effectiveness
Low overall equipment effectiveness (OEE) can signal inefficiencies in production and negatively impact output. Monitoring OEE enables manufacturers to identify and eliminate waste.
- Invest in Monitoring Tools: Employ tools to continuously track OEE and provide insights into performance metrics.
- Identify Bottlenecks: Use OEE data to pinpoint bottlenecks and inefficiencies in the production line, facilitating targeted interventions.
- Implement Continuous Improvement Programs: Foster a culture of continuous improvement to inspire innovation and optimization in equipment use.
5. Inspection Speed
Slow inspection processes can create bottlenecks in production, leading to delays and decreased throughput. Streamlining inspection without compromising quality is vital.
- Optimize Inspection Layout: Design a production layout that minimizes travel time and enhances workflow efficiency during inspections.
- Automate Inspection Steps: Integrate automated vision systems to significantly speed up the inspection process without sacrificing quality.
- Reduce Changeover Times: Implement strategies to minimize changeover times for quicker transitions between different inspections.
6. Operator Training Efficiency
Ineffective operator training can lead to mistakes and inconsistency in inspections, ultimately affecting product quality. Investing in efficient training methods is essential for long-term success.
- Develop Comprehensive Training Programs: Create and regularly update training programs that address all aspects of quality inspection processes.
- Use Hands-On Training Techniques: Incorporate hands-on training that allows operators to practice using the equipment under real-world conditions.
- Evaluate Training Impact: Assess the effectiveness of training programs through evaluations and feedback to continuously enhance the training experience.
7. System Integration
Poorly integrated inspection systems can lead to disruptions and miscommunication between different stages of the manufacturing process. Ensuring seamless integration is vital for efficiency.
- Assess Compatibility: Evaluate the compatibility of your vision systems with existing equipment and software to facilitate smooth integration.
- Collaborate with Experts: Partner with experienced system integrators who can ensure that all components function harmoniously.
- Conduct Thorough Testing: After integration, carry out extensive testing to ensure all systems are operating efficiently and effectively together.
8. Data Analysis
Many manufacturers overlook the importance of data analysis, leading to missed opportunities for optimization and understanding inspection performance. Harnessing data can drive significant improvements.
- Implement Data Collection Systems: Set up systems to collect and analyze inspection data in real-time for informed decision-making.
- Use Analytics Tools: Leverage advanced analytics tools to uncover insights and trends that can guide quality improvement strategies.
- Share Insights Across Teams: Ensure insights from data analysis are communicated across relevant teams to drive collaborative improvements.
9. Regulatory Compliance
Failure to comply with industry regulations can result in costly penalties and damage to reputation. Establishing processes for ongoing compliance is crucial for any manufacturer.
- Stay Informed on Regulations: Regularly update your knowledge of current regulations to ensure your inspection processes meet or exceed compliance standards.
- Conduct Compliance Audits: Perform regular audits of quality inspection processes to identify potential compliance gaps.
- Document Compliance Efforts: Maintain thorough records of compliance efforts as evidence during regulatory inspections or audits.
10. Cost Savings
High operational costs can erode profit margins and impede growth, making it essential for manufacturers to identify cost-saving opportunities within their inspection processes. Focusing on cost efficiencies can significantly enhance bottom lines.
- Evaluate Inspection Costs: Analyze current inspection costs to identify areas where efficiencies can be achieved and expenses reduced.
- Invest in Quality Technologies: While it may require upfront investment, adopting advanced inspection technologies can lead to significant long-term cost savings.
- Benchmark Against Industry Standards: Compare your inspection costs with industry benchmarks to identify underperforming areas and set realistic savings goals.